The process begins by removing the bottle crates from the pallets and placing them in the unpacking machine. Then the bottles are separated from the boxes and taken to the Crate Washers. In this machine, the bottles go through different temperatures and detergent solutions to finally be rinsed with jets of freshwater at different pressure process that assures us to have impeccable bottles.
Subsequently, a conveyor belt moves the bottles clean and still empty, for strict quality control through electronic inspectors provided with optical sensors that check every small detail or imperfection and automatically separate the bottles that do not meet the appropriate conditions.
Once the electronic inspector has selected the bottles, they go to the packaging machines to be filled and capped. The Bottle Loaders have vacuum pumps, pressure recorders, and implements of great precision and modernity that ensure a continuous, efficient, and quality process.
Once we have filled and capped bottles, we go to the pasteurization process, where the biological stability of the product is ensured through different temperature changes.
Each of the bottles is then identified by placing labels and the date of packaging.
Finally, the bottles already labeled are introduced in plastic boxes through automated machines. The boxes with the product are placed on pallets or pallets to be taken to the warehouse where they are stored and are ready to be transported to the various points of sale in the country.
Distribution: its distribution centers integrate employees, materials, machinery, auxiliary activities, and any other factor so that the best compromise between all these parties that complement the distribution results.
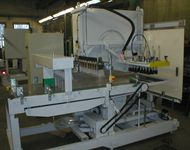
The trucks, an important point of the distribution area, comply with a sophisticated design and have a modern bodywork that allows increasing the productivity in the loading and unloading of products with Bottle Unloaders. This system reduces the operating time, both in small stores and in stores — supermarkets, where we now focus our effort to efficiently and effectively meet your product requirements.
Aware of the responsibility of the community, the new trucks are equipped with an electronic speed limiter. They also have an additional engine brake to the service brakes, making them safer and minimizing the risk of traffic accidents.
PROBLEMS DETECTED
- Lack of bottles: The lack of bottles in the packaging process is a problem that must be addressed urgently, since the lack of elements like this is a sign that there is a lack of organization, planning, inventory, lack of communication between departments, Between the company and the suppliers. The lack of bottles at the time of filling these causes a delay in the process, resulting in the loss of time, loss of money, because all this provides time and money for the development of a product. But we must look for the specific causes that cause the raw material is not just in time.
- Lack of labels: This is another bottleneck found in the National Brewery in the packaging area, a situation that causes the product to be unavailable for the distribution of bottles, in addition to gaining a bad image before its customers since Your product is not delivered in the required time.